Today’s pressures in design and development have led to an increased interest in more precise construction techniques. With the rising demands on project schedules and building performance, offsite fabrication of building components is gaining popularity.
Prefabrication and modular construction have been around for decades. However, with recent advances in technology, better design tools and the pressure of tighter project timelines and requirements, fabrication systems have become more common in manufacturing. Industries such as automobiles and electronics have proven that safety, speed and quality can all be improved through the adoption of automated fabrication. The construction industry, historically slow to change, is now adapting these processes to improve the quality of the built environment.
There are currently three main systems that are being employed as common techniques in manufacturing for design and construction. The major systems are custom fabrication of building elements, panelized systems and modular construction.
These approaches, while different in scale and application, have key similarities. Each one benefits from a precise fabrication process in a controlled environment and a more efficient process that systemizes the construction process to minimize waste which, in the end, produces a high-quality built project. Each of these approaches also has significant differences that need to be understood to determine which method is most appropriate for a particular project.
Custom fabrication of building components (also called mass customization) allows the custom design of building components through collaboration between designer and fabricator. Building elements like the kinetic façade at the recent addition to the Central Garage at Logan Airport and the soffit at Congress Square are examples of this type of fabrication. Large building components, imagined by the design team, can be designed digitally and shared directly via 3D virtual models with fabricators – removing the constraints of traditional drawing methods for unique and exciting results.
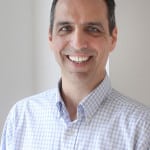
David Bois
A Constrained Hotel Site in Boston
Panelized systems include the construction of complete walls off site. These exterior wall panels include exterior finish, windows, weatherproofing and insulation, and can be built at the same time the project itself is being erected. Panels are then transported to the site at the optimal time and installed directly onto the structural frame.
The hotel under construction at 54 Devonshire is an example of this type of construction. The small site in the heart of downtown Boston would have been even more constrained by scaffolding and materials storage that would have been needed for traditional construction methods. For this project, the brick, metal and glass facades were fabricated on lightweight steel frames at an offsite fabricator while the concrete of the building was being poured. The panels were installed over a period of just 13 days, completely enclosing the building in less than two weeks which enabled the interior finishes to move forward in a weather-protected environment.
Modular construction, used for decades in single-family homes, has seen recent popularity in commercial construction, especially in multifamily wood frame residential projects. This approach involves the construction of complete sections of the buildings – structure, partitions, exterior and interior finishes, mechanical, plumbing and electrical systems.
Foundation and site construction proceeds in a more typical fashion, with modules transported to the site and then stacked together to create the building. The primary limitation on this type of construction is in the transportation of the modules – which in most cases need to be transported on public highways. The approach is currently utilized more effectively in wood construction, but European models with steel and concrete have the potential to expand the application of these systems.
As architects, we are continually challenged to find techniques that allow for the development of buildings that perform better, reduce waste and can be delivered more efficiently. Understanding fabrication and mass customization techniques and implementing these early in the design process allows for the expression of unique design elements while addressing the owner’s needs for predictability and performance.
David Bois is a principal at Arrowstreet Architecture and Design.